Why plastic extrusion is perfect for mass production
A Comprehensive Guide to the Refine and Advantages of Plastic Extrusion
In the vast realm of manufacturing, plastic extrusion arises as a necessary and very effective process. Altering raw plastic right into continuous profiles, it provides to a huge selection of sectors with its amazing adaptability.
Understanding the Fundamentals of Plastic Extrusion
While it might appear facility in the beginning glance, the procedure of plastic extrusion is fundamentally basic - plastic extrusion. It is a high-volume production strategy in which raw plastic is thawed and shaped into a constant account. The process begins with the feeding of plastic material, in the form of powders, granules, or pellets, right into a warmed barrel. The plastic is then thawed using a combination of warmth and shear, used by a rotating screw. When the molten plastic gets to the end of the barrel, it is required via a tiny opening called a die, shaping it into a preferred type. The designed plastic is after that cooled, solidified, and reduced right into wanted lengths, completing the procedure.
The Technical Refine of Plastic Extrusion Explained
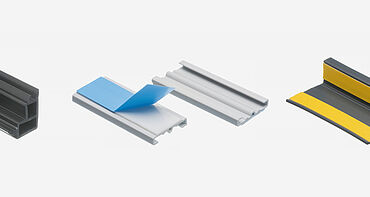
Kinds of Plastic Suitable for Extrusion
The selection of the appropriate kind of plastic is an essential aspect of the extrusion process. Various plastics offer unique properties, making them a lot more suited to certain applications. Polyethylene, for instance, is generally used because of its reduced price and easy formability. It offers excellent resistance to chemicals and dampness, making it perfect for products like tubes and containers. Similarly, polypropylene is another preferred option as a result of its high melting point and resistance to exhaustion. For more robust applications, polystyrene and PVC (polyvinyl chloride) are typically picked for their strength and sturdiness. Although these are typical choices, the option inevitably depends on the particular requirements of the product being produced. So, comprehending these plastic types can dramatically improve the extrusion procedure.
Comparing Plastic Extrusion to Other Plastic Forming Methods
Recognizing the types of plastic appropriate for extrusion leads the way for a wider discussion on just how plastic extrusion stacks up versus other plastic forming techniques. These consist of injection molding, blow molding, and thermoforming. Each method has its unique usages and advantages. Shot molding, for instance, is excellent for creating detailed parts, while strike molding is excellent for hollow things like containers. Thermoforming excels at forming shallow or huge parts. Plastic extrusion is exceptional when it comes to developing constant accounts, such as pipes, seals, and gaskets. It also enables a regular cross-section along the from this source length of the item. Hence, the selection of technique largely depends upon the end-product requirements and requirements.
Secret Advantages of Plastic Extrusion in Manufacturing
In the realm of production, plastic extrusion offers many considerable benefits. One notable advantage is the cost-effectiveness of the procedure, that makes it an economically attractive production method. Additionally, this method gives remarkable item adaptability and enhanced manufacturing rate, thus raising total production efficiency.
Cost-Effective Production Approach
Plastic extrusion leaps to the center as an affordable manufacturing method in production. Furthermore, plastic extrusion calls for much less power than typical production techniques, contributing to reduced operational expenses. Generally, the economic benefits make plastic extrusion an extremely appealing option in the manufacturing market.
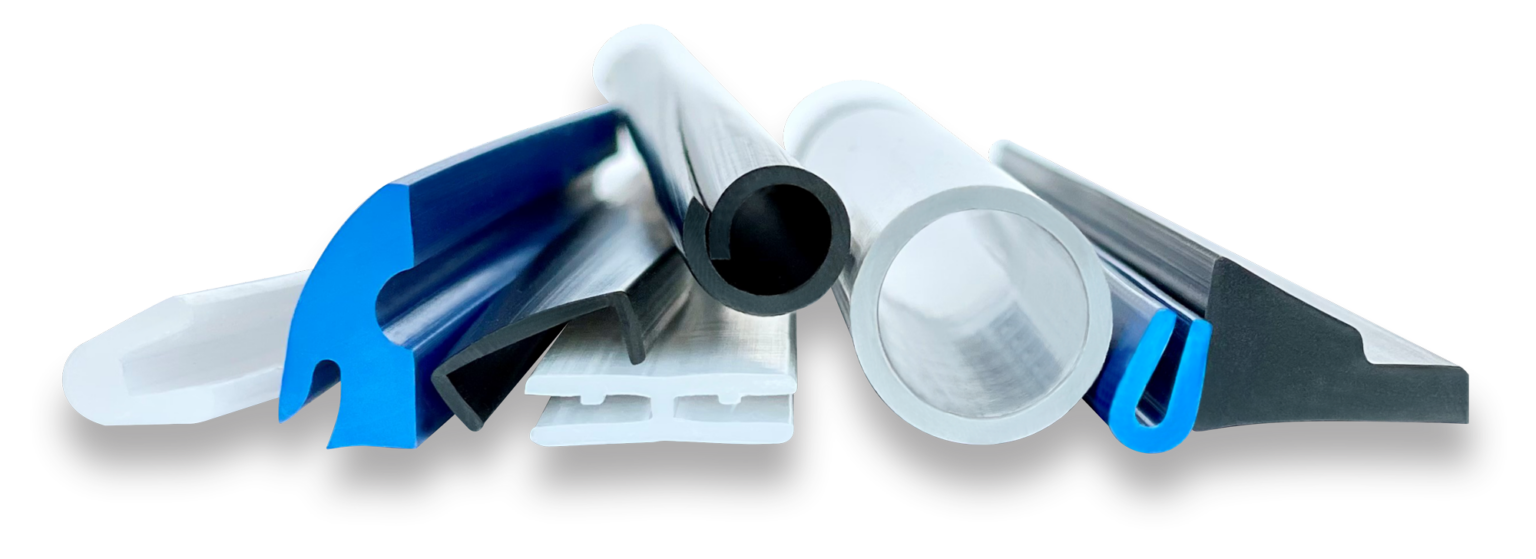
Superior Product Versatility
Beyond the cost-effectiveness of plastic extrusion, another significant benefit in manufacturing lies in its exceptional product versatility. This makes plastic extrusion an excellent service for markets that need tailored plastic parts, such as automotive, building, and product packaging. In essence, plastic extrusion's product flexibility promotes innovation while improving operational efficiency.
Improved Manufacturing Rate
A significant advantage of plastic extrusion exists in its enhanced production rate. Couple of other production processes can match the speed of plastic extrusion. Additionally, the capability to keep regular high-speed production without sacrificing product quality establishes plastic extrusion apart from various other techniques.
Real-world Applications and Impacts of Plastic Extrusion
In the world of production, the strategy of plastic extrusion holds extensive significance. The economic benefit of plastic extrusion, largely its high-volume and economical output, has changed production. The see this website industry is persistently striving for developments in eco-friendly and recyclable materials, suggesting a future where the advantages of plastic extrusion can be maintained without endangering environmental sustainability.
Final thought
To conclude, plastic extrusion is a highly efficient and effective method of transforming raw materials into diverse products. It offers many benefits over other plastic forming methods, consisting of cost-effectiveness, high outcome, minimal waste, and layout adaptability. Its impact is exceptionally felt in various sectors such as construction, automobile, and durable goods, making it a pivotal procedure in today's manufacturing landscape.
Digging deeper right into the technological procedure of plastic extrusion, it begins with the selection of the suitable plastic material. Once cooled down, the plastic is cut into the required sizes or injury onto reels if the item is a plastic film or sheet - plastic extrusion. Contrasting Plastic Extrusion to Various Other Plastic Forming Methods
Understanding the kinds of plastic suitable for extrusion leads the my company way for a more comprehensive conversation on exactly how plastic extrusion stacks up versus other plastic forming approaches. Couple of other production processes can match the rate of plastic extrusion.